By Sim Tze WeiAssociate Foreign News Editor, Lianhe Zaobao
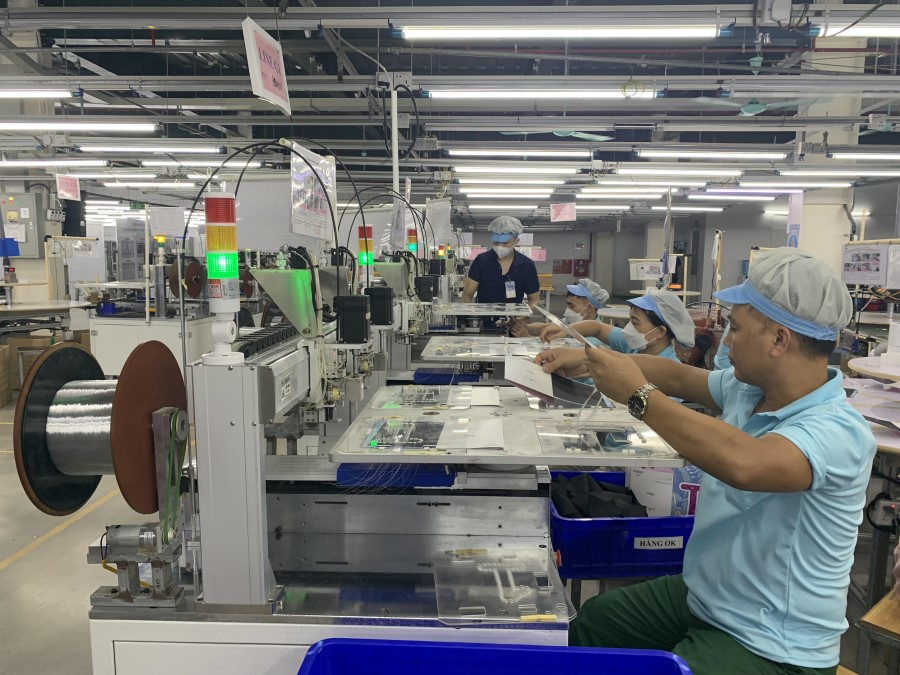
Superior EMS’s factory in the Vietnam-Singapore Industrial Park in Hai Duong province. It is using small modular machinery to automate its production lines. (SPH Media)
Headlines such as “Vietnam’s exports overtake Shenzhen” and “Is Vietnam the next China?” have drawn attention in China’s media and online forums, reflecting anxiety that Vietnam might usurp China’s position as the world’s factory.
Western media, meanwhile, have focused on how China’s zero-Covid policy has caused orders to be diverted to Vietnam. In a June report by German newspaper Frankfurter Allgemeine Zeitung with the eye-catching headline “Goodbye China, Hello Vietnam”, one manufacturer said, “Vietnam seems to be a better and cheaper China.”
In the second quarter of 2022, Vietnam’s exports rose 21% year-on-year and economic growth hit an 11-year high of 7.7%. The country has emerged from last year’s slump, when lockdowns in several cities – including the capital Hanoi – caused GDP to shrink 6.2% in the third quarter.
With its land border with China and a coastline of over 3,000 km, Vietnam has a highly strategic location and an advantage in maritime logistics.
After Vietnam’s government pushed mass vaccination in a bid to coexist with the virus, the full resumption of factory operations and border reopening enabled a rapid rebound. The contrast with China’s zero-Covid stance propelled Vietnam into the spotlight, with some international media hailing it as the new “Super Factory”.
Top choice for a ‘China+1’ strategy
Business owners and executives of foreign enterprises in Vietnam told Lianhe Zaobao that a few years before the pandemic, Vietnam was already emerging as a key beneficiary of the China-US trade tensions that began in late 2018. Many foreign companies started to mitigate supply chain risks by setting up manufacturing operations in nearby Vietnam, or diverting orders there from China.
With its land border with China and a coastline of over 3,000 km, Vietnam has a highly strategic location and an advantage in maritime logistics. Other factors making it attractive for a “China+1” strategy are cheap labour, young demographics, favourable policies, free trade agreements with several countries, and friendly relations with both China and the US.
Superior EMS, from Hong Kong, is one foreign manufacturer that set up in Vietnam to spread its risk. Director Charles Wong met Lianhe Zaobao at the company’s factory in Hai Duong province, about one-and-a-half hour’s drive from Hanoi. With Superior having invested in China for over two decades, the similarities between China’s and Vietnam’s systems were one reason to enter the latter. “It’s easier for us to adapt,” he said.
Superior’s main business is toy production and production line automation. It has two factories in the southern Chinese city of Dongguan, and a plant in the Vietnam-Singapore Industrial Park (VSIP) in Hai Duong, operating since March 2020. It makes high-end technology products in China, and simpler products in Vietnam.
Superior’s decision to set up in Vietnam was customer-driven, Wong said. Many clients started shifting their operational focus to Southeast Asia three to four years ago, and set new requirements for supply chain security.
“They’re worried that problems in one place might cause a breakdown in the supply chain,” he said. “If suppliers have factories in different countries, supply would be more secure.”
… for March alone, the gap was US$34.62 billion, with Vietnam’s exports almost twice that of Shenzhen’s.
Gaining from China’s zero-Covid policy
The China-US trade war triggered the first recent wave of shifts. Now the world has noted how China’s zero-Covid policy has led to prolonged production shutdowns. Once businesses – both foreign and Chinese – decide to relocate, will Vietnam benefit from a second “China +1” wave?
According to Vietnam News Agency, the country received US$7.7 billion in foreign direct investment in the first five months of 2022, up 7.8% year-on-year. For the first quarter of 2022, Vietnam’s total exports exceeded Shenzhen’s by US$27.75 billion; for March alone, the gap was US$34.62 billion, with Vietnam’s exports almost twice that of Shenzhen’s.
Singapore’s Sembcorp Development has been involved in managing the Vietnam-Singapore Industrial Parks (VSIPs) since the first was launched in 1996, with 10 across Vietnam now.
Kelvin Teo, CEO of Sembcorp Development and co-chairman of the VSIP Group, said that as of 31 December 2021, the VSIPs have attracted 850 companies with total investment capital of US$15.6 billion. From 2017 to 2021, the parks saw 104 entrants and new investments totalling US$400 million.
Teo said that it was hard to pinpoint flows from mainland China, as there are different possible channels: via Hong Kong; through origin countries of mainland-based foreign enterprises; or through joint ventures with Vietnamese enterprises. “But we can assume that the Chinese are part of the increase in investments into Vietnam over the years,” he shared.
While the VSIP has been receiving enquiries about investing in Vietnam, he is “not able to ascertain if these are due to the Covid-19 situation in China”.
Chien Chih Ming, chair of the Taiwanese Chamber of Commerce in Vietnam, noted an increase in enquiries from Taiwanese firms looking to invest in Vietnam – including some based in mainland China. He said, “If the factory stops work completely because of the pandemic, and the boss has to keep paying salaries, interest and loan instalments, which company can survive this?”
The interview with Chien took place in Dong Nai’s industrial zone, about one-and-a-half hour’s drive from Ho Chi Minh City, where the construction firm he set up over 10 years ago is headquartered. In the early days, both Dong Nai and Hai Duong drew traditional industries such as textiles and shoe-making companies, many relocating from China.
About four to five years ago, a wave of companies – led by electronics manufacturers – moved operations from China to Vietnam to diversify supply chain risks amid the China-US trade war, clustering in the north around Hanoi.
As Vietnam has a long and narrow land mass, the north benefited from its proximity to China. Electronics manufacturers could send required parts and materials overland from China’s south-eastern coast.
Much of [Vietnam’s manufacturing] involves the assembly and packaging of what was “Made in China”, before the finished product is labelled “Made in Vietnam” to avoid tariffs, and exported to the US and Europe.
Smartphone giants such as South Korea’s Samsung and Apple’s supplier Foxconn continuously expanded in northern Vietnam; Taiwan’s Pegatron and Wistron, alongside other electronics giants, have also increased their investment. Recently, China’s Xiaomi confirmed that it would start making phones in Vietnam too. Vietnam has become a manufacturing hub for mobile phones and computer peripherals.
Chinese orders create headaches
However, the pandemic laid bare the vulnerability of this cross-border chain.
Vietnam’s export-oriented, processing-focused manufacturing has a heavy upstream reliance on China. Much of it involves the assembly and packaging of what was “Made in China”, before the finished product is labelled “Made in Vietnam” to avoid tariffs, and exported to the US and Europe.
The problem comes when components fail to arrive from China, severely curtailing Vietnam’s ability to fulfil export orders.
At the start of 2020, pandemic-induced land transport curbs forced Samsung to fly smartphone parts from China to Vietnam to avoid a complete supply chain breakdown.

Taiwanese companies in Vietnam found it hard to be happy about the surfeit of orders, said Chien, as upstream supply disruptions in mainland China caused delays in order fulfilment. Raw material costs also rose with oil prices, eating into margins; businesses were in a difficult position whether they had orders or not.
Wong’s toy factory faced the same issue after Chinese New Year, and had to send components from China to Vietnam via sea or air. But as all manufacturers were turning to these alternatives, demand for such freight surged, affecting availability.
Supply bottlenecks drive localisation
Crises give rise to new ideas. Wong decided to overcome upstream bottlenecks by localising intermediate goods.
In the past, intermediate or semi-finished products arrived from the company’s plant in Dongguan for processing in Vietnam; now, the company plans to import material to be stored in Vietnam. Once orders are received, the whole production process – from manufacturing of parts to assembly – will be completed at the Vietnam factory.
Norman Lim, president of the Singapore Business Group in Ho Chi Minh City, is also the Asia Pacific CEO of a foreign-funded manufacturer of industrial blades. In an interview at an industrial park in Ho Chi Minh City, Lim said that his employer also experienced supply chain problems in China during the pandemic.
To spread the risk, it decided to source for raw materials from places such as Thailand, Taiwan and India. Lim said, “I believe many plants like ours will continue to search for replacement sources of raw material outside of China.”
No easy feat to usurp China’s position
As more Vietnam-based manufacturers seek intermediate goods from outside China, and as the supply chains of more industries mature, will Vietnam be able to usurp China’s position as the world’s factory?
Business leaders interviewed were unanimous in their verdict: “Impossible.”
In the early days, Vietnam could attract only the pollutive parts of supply chains in traditional industries that were being phased out in China.
Lim noted that industries were not relocating exclusively to Vietnam, with other destinations including India and Southeast Asian countries such as Indonesia, Malaysia, Thailand, the Philippines and Laos. “You can replace China only by adding up many different countries together.”

Vietnam’s population of nearly 100 million is only a tenth of China’s, he added. The middle class is expanding rapidly, pushing wages up and nudging industries from developed areas into poorer ones. While China’s development moved from east to west, Vietnam does not have a comparable hinterland.
Chien observed that China has the advantage of comprehensive industrial chains, and its capacity for administrative organisation outstrips that of Vietnam. In the early days, Vietnam could attract only the pollutive parts of supply chains in traditional industries that were being phased out in China. Even the electronics activities that have recently moved from China are primarily in low-end manufacturing.
While China has higher labour costs, Chinese workers have better skills and expertise. And while Vietnamese workers are diligent, Chien had this observation to make: “If you say the Vietnamese are extremely hardworking, the Chinese work themselves to the ground.”
ISEAS-Yusof Ishak Institute senior fellow Jayant Menon observed that although China’s lockdowns have hastened the pre-pandemic shift to Vietnam, regional supply chains remain very much China-centric, and this is likely to continue for the foreseeable future. Menon added, “China remains a manufacturing giant and therefore you cannot contain or replace it easily.”